|
 |
|
|
|
CEMENT
PLANTS
Rotary Kiln Cement Plants
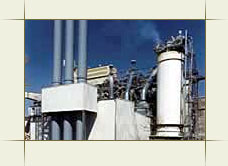 |
Sabko Industries Group offers Rotary kiln Cement plants that speaks innovation, quality
conscious and cost effective technology. We offer Medium size to Large Size ROTARY KILN
Cement plants from 600 TPD to 6500 TPD on turn key basis
and have capabilities to undertake all aspects of project
including, feasibility studies, technical
advice, equipment supply, field construction, erectioning, supervisory
services, commissioning etc.
|
So
that the dust does not escapes into the environment
highly efficient measures for pollution control have
been incorporated in every cement plant. Every material transfer points
is installed with Reverse pulse jet filters,
innovative bag filters and other most modern
environmental friendly pollution control equipments. Electro
static precipitator (ESP) treats the Fuel gases from kiln
for cleaning before discharging into the atmosphere helping to maintain the eco friendly environment.
High efficiency Bag Houses are also incorporated
to meet the local environmental laws.
View Rotary Kiln Plant I
View Rotary Kiln Plant II
CLICK HERE TO
UNDERSTAND

|
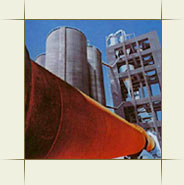 |
|
|
Unique
Features
|
- Low
pressure drop pre heaters.
- Raw mill
equipped with High efficiency separator.
- Raw
Meal blending in CFC silo.
- Pre-calciner suitable to work with alternative fuels.
- Inlet &
discharge fitted with Efficient seals.
- Benchmark
cooler design.
|
|
|
Benefits
|
- Near Zero
Maintenance.
- Operation
of Plant is Simple.
- Gestation
period is short.
- Greater efficiency in
Power Consumption .
-
Abundant
fuel savings.
- Low
Installed cost.
- Trusted and proven
Trouble free Technology.
|
|
|
|
Plant
Picture Gallery |
|
|
|
Cement Manufacturing Process |
1.
Crushing & Proportioning:
Limestone rock is the principal raw material, the
first step after quarrying in the processes is the
primary crushing. Mountains of rock are fed
through crushers capable of handling pieces as
large as an oil drum. The first crushing reduces
the rock to a maximum size of about 150 mm. The
rock then goes to secondary crushers or hammer
mills for reduction to about 75 mm or smaller.
After that the material is stacked with the help
of a stacker and reclaimed with the bridge type
reclaimer in a cross section so that the
homogeneous limestone is fed further in the
process, thus averaging the limestone quality.
2.
Raw milling &
Blending:
The next step in the process is to grind the above
particles to a size of 90 microns or less which is
done in a raw mill, a closed circuit ball mill
equipped with high efficiency separator. After
achieving the 90 microns size the fine grinded
material also known as raw meal is sent to the
continuous blending silos (CFC) for homogenization
& extracted by means of load cell hopper for the
next step which is feeding to the kiln pre
heaters.
3. Pyro processing:
The raw material is heated to exceeding 1,450 °C
(2,700 degrees F) in 5 or 6 stage pre-heater tower
(about 110 metres in height) in the suspended
form, than through a pre-calciner and finally in a
huge cylindrical steel rotary kilns lined with
special firebrick. Kilns are frequently as much as
3.7 M (12 pi) in diameter, large enough to
accommodate an automobile and longer in many
instances than the height of a 40-story building.
Kilns are mounted with the axis inclined slightly
from the horizontal. The finely ground raw
material or the slurry is fed into the higher end.
At the lower end is a roaring blast of flame,
produced by precisely controlled burning of
powdered coal, oil or gas under forced draft.
4. Burning and
cooling:
As the material moves through the kiln, certain
elements are driven off in the form of gases. The
remaining elements unite to form a new substance
with new physical and chemical characteristics.
The new substance, called clinker, is formed in
pieces about the size of marbles.
Clinker is discharged red-hot from the lower end
of the kiln and generally is brought down to
handling temperature in Grate coolers. The heated
air from the coolers is returned to the kilns, a
process that saves fuel and increases burning
efficiency.
5. Cement milling,
Storage & Packing:
Portland cement, the basic ingredient of concrete,
is a closely controlled chemical combination of
calcium, silicon, aluminum, iron and small amounts
of other ingredients to which gypsum is added in
the final grinding process to regulate the setting
time of the concrete. Lime and silica make up
about 85% of the mass. Common among the materials
used in its manufacture are limestone, shells, and
chalk or marl combined with shale, clay, slate or
blast furnace slag, silica sand, and iron ore. The
above mixture
|
Rotary Kiln Cement Plant Project at a Glance
|
|
Plants Offered |
600 |
900 |
1200 |
1500 |
2500 |
3000 |
4500 |
5500 |
6500 |
Land area
required (Sq. M) |
80,000 |
100,000 |
125,000 |
175,000 |
280,000 |
325,000 |
450,000 |
550,000 |
650,000 |
Captive
Power Requirements (KW) |
6000 |
8500 |
10,000 |
12,500 |
22,500 |
27,500 |
40,500 |
49,500 |
58,500 |
Project
Lead time (months) |
16 - 18 |
16 - 18 |
16 - 18 |
22-26 |
22-26 |
22-26 |
32-38 |
32-38 |
32-38 |
|
Raw
Material Requirements (Tons Per Day) |
Lime Stone |
900 |
1,350 |
1,800 |
2,250 |
3,750 |
4,500 |
6,750 |
8,250 |
9,750 |
Clay |
90 |
135 |
180 |
225 |
375 |
450 |
675 |
825 |
975 |
Coal (4500
kcal/kg) |
120 |
180 |
240 |
300 |
500 |
600 |
900 |
1,100 |
1,300 |
Gypsum
(approx. 5%) |
30 |
45 |
60 |
75 |
125 |
150 |
225 |
275 |
325 |
|
Manpower (for 3 shift) |
Administrative & Managerial |
7 |
7 |
10 |
10 |
12 |
15 |
15 |
18 |
18 |
Technical &
Laboratory |
15 |
15 |
18 |
20 |
24 |
25 |
25 |
28 |
28 |
Skilled
Workers & Front Line
Managers |
15 |
15 |
18 |
22 |
25 |
28 |
28 |
30 |
32 |
Unskilled
Workers |
36 |
36 |
44 |
50 |
60 |
65 |
65 |
70 |
70 |
|
Utilities |
Power
(KWH/T) |
100 - 110
|
100 - 110
|
100 - 110
|
90 - 100
|
80 - 90
|
80 - 90
|
80 - 90
|
80 - 90
|
80 - 90
|
Fuel
(kcal/kg) |
850 - 900
|
850 - 950
|
800 - 850
|
750 - 800
|
750 - 800
|
750 - 800
|
750 - 800
|
750 - 800
|
750 - 800
|
|
|
|
IN ACTION |
|
 |
|
|
|
|